The Code shows the way forward
SCA has worked intensively to increase awareness of ethical issues in the organization, using the Code of Conduct to support its efforts. Sound business practices, good working conditions and respect for human rights have been a few of the company’s focus areas. Training and supplier audits are tools to help the company achieve its targets.
Training in the Code
SCA’s Code of Conduct is a tool for inspiring confidence in the Group, something we earn by responsibly managing our stakeholder relationships. Since 2004, our Code of Conduct has helped translate SCA’s core values of respect, responsibility and excellence into action. In 2014, a campaign was carried out to ensure that all employees received training in the Code. Providing training and information about the Code is a continuous process that is never truly finished.
Choosing the right partners
The more SCA grows at global level, the more important it becomes for the Group to review its local suppliers and choose responsible business partners. The aim is to identify risks and develop the social and environmental performance of suppliers.
SCA’s objective is to drive shared values and priorities throughout the supply chain in line with SCA’s Global Supplier Standard. During the year, a risk analysis was carried out with a focus on handling recovered fiber, which resulted in the introduction of a recognition program for suppliers in Mexico.

TARGET
We will maintain compliance with our SCA Code of Conduct. All employees will receive regular training in the Code.
Our SCA supplier standard will be used to drive shared values and priorities throughout our supply chain.
OUTCOME 2015
91% of employees have received Code of Conduct training.
84% (75) of SCA’s global hygiene supplier base and 86% (83) of the forest product’s supplier base had signed the SCA Global Supplier Standard.
Competing on the right terms
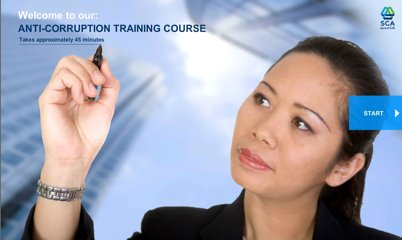
Free and fair competition is an important cornerstone in every society, and for every sustainable business operation. SCA has a long-standing training program for employees who, during the course of their work, encounter and require extra expertise when it comes to issues concerning competition law.
As part of the program, employees receive written guidelines and an opportunity to participate in recurring training seminars in small groups, during which various relevant issues are discussed. During the year, SCA also introduced a new, interactive e-learning program addressing all areas of competition law.
To ensure that employees understand all of the rules and regulations, the program also includes a section in which they must answer various questions. More than 2,000 employees took part in this program during the year.
Whistleblowing in Latin America
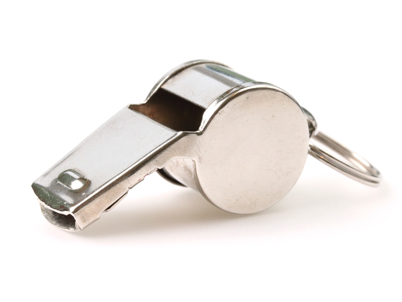
SCA is testing a new whistleblowing system in Mexico. Individuals who witness improprieties or unacceptable behavior within SCA can report it in their local language through a website or by telephone. The reports are received by an external party that registers the case.
The identity of the whistleblower is always protected, regardless of whether he/she chooses to be anonymous. The whistleblower can follow his/her case by logging into the website.
“We want to examine the effectiveness of an external hotline as a complement to the internal whistleblowing system that is already in place,” explains Lulu Li, Corporate Social Responsibility Manager at SCA.
“We have a similar pilot project in the UK, but wanted to test the system in one of our emerging markets, in this case, Mexico.”
SCA is creating awareness of the new channel through an information campaign, using media such as posters, articles on the intranet and advertisements in staff magazines. So far, a handful of reports have been received during the year. In late 2015, SCA decided to introduce similar whistleblowing systems in Central America, Chile and Brazil.
Satisfied employees
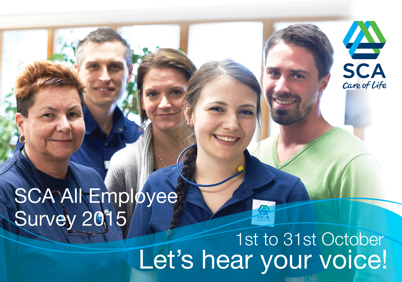
SCA’s 2015 All-Employee Survey showed excellent results with improvements in all areas and an all-time-high response rate of 88.3%.
The All-Employee Survey is carried out every second year. This was the third survey in the company’s history and gradual improvements have been noted in each of the surveys. The overall SCA Index was 72 (maximum score of 100), an improvement of 2 points compared with 2013.
“The 2015 survey results underline our positive company culture, which continues to be something that we can be truly proud of,” says Anna Sävinger Åslund, SVP Human Resources. “As before, we can see a high level of engagement throughout the organization.”
A continued improvement was seen in all global results. This is especially true for those areas on which SCA has chosen to focus at a global level, for example, leadership, professional development, information concerning the strategy and changes, and occupational safety. The results are followed up in the form of workshops and actions plans in all units. More data about the All-Employee Survey can be found in chapter Value creation for people – Employee relations.
Supplier program in Mexico
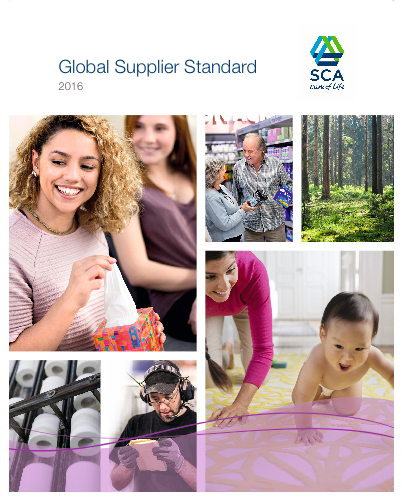
SCA’s Global Supplier Standard was updated in 2015.
SCA uses recovered fiber in parts of its operations. SCA is well aware of the risks related to, for example, health and safety, working conditions, child labor and forced labor that may arise when sourcing recovered fiber from high-risk areas. The company works to minimize the risks related to recovered fiber sourcing.
One example of how SCA works to mitigate risks is the voluntary Mexico Supplier Recognition Program, which has been developed during 2015 for rollout in 2016. The program has a three-pronged approach: 1. Suppliers commit to the criteria in SCA’s Global Supplier Standard. 2. A product and raw material specification regulates SCA’s recovered fiber criteria. For example, SCA does not approve fiber materials from landfill. 3. Suppliers commit to following a program for improved health and safety, and labor conditions for employees.
The supplier program was preceded by a pilot program with a number of suppliers from Mexico City.
“We learned that suppliers are eager to partner with a strong company like SCA, not only to improve their health and safety, but also quality and business development,” says David Knight from SCA.
The lessons learned from the pilot project were used to develop the Mexico Supplier Recognition Program.
“The reaction so far has been very positive; every supplier we have approached has signed up. They appreciate our concern and help in becoming more responsible,” says David Knight. The goal is to involve 70% of SCA’s recovered-fiber suppliers in 2016. Read more about SCA’s fiber sourcing initiatives.